NYHET
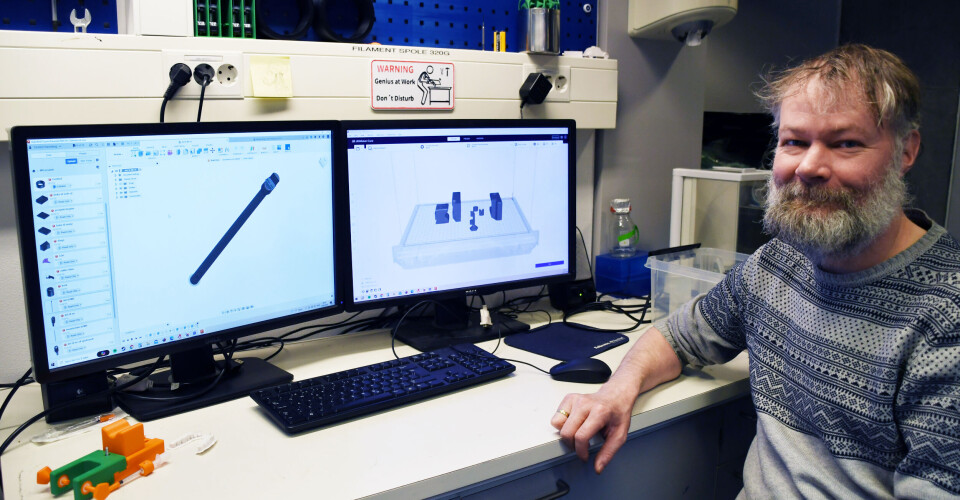
Sparer miljøet på å lage utstyrsdeler selv
Ved hjelp av en 3D-printer kan Institutt for biomedisin lage nye deler selv når utstyr går i stykker. Dette reduserer miljøutslipp i tillegg til at utstyr får lengre levetid.
Teknisk fellesavdeling ved Institutt for biomedisin søkte Klimafondet ved UiB om midler til å kjøpe en ny 3D-printer. De hadde gode erfaringer med en tidligere prototype, men som begynte å bli gammel og manglet presisjonen de trengte.
– Istedenfor å bestille deler til forskjellig utstyr, kan vi kan lage dem selv. Det sparer blant annet miljøet for utslipp gjennom frakt via ulik transport, sier forskningstekniker Stein Rune Lindhom på instituttet.
Søk om midler fra Klimafondet – frist 17. mars
Får lengre levetid
Gjennom 3D-printeren kan de hjelpe de ulike forskningsgruppene på Institutt for biomedisin, men også blant andre Kvinneklinikken på Haukeland.
Noe de har lagd er for eksempel deler til inkubatorer som manglet låser på Kvinneklinikken, til ødelagte bur for forsøksmus, og et treningsapparat i kjelleren.
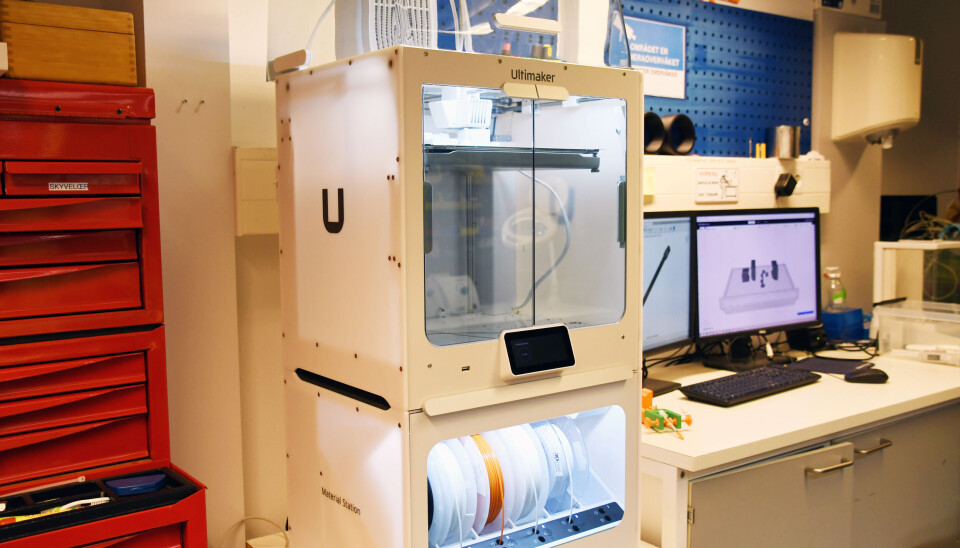
Mye av det vi lager er små, unnseelige deler til maskiner som vi ikke får tak i lenger
Forskningstekniker Hans Martin Vikse
– Mye av det vi lager er små, unnseelige deler til maskiner som vi ikke får tak i lenger, som en liten knott som ryker. Når for eksempel en sentrifuge er 20 år gammel, så selges ikke delene lenger, forklarer forskningstekniker Hans Martin Vikse.
Dette gjør at utstyr får lengre levetid på instituttet enn det ellers hadde fått, som er bra for miljøet. Alternativet er ofte å kjøpe en helt ny maskin.
Utfordrende med små rundinger
Forskningsteknikerne bruker et eget designprogram på PC-en til å tegne av delene de trenger. Iblant finner de også design som andre har delt på egne nettportaler.
De kan lage deler av plasttyper i ulik hardhet, som PLA, TPU og ABS.
– Å lage små rundinger er nok det mest utfordrende. Printerhodene går egentlig i firkanter. Jo mindre størrelse du trenger, jo vanskeligere er det å lage den. I tillegg krymper plasten etterpå, og det må du ta høyde for. Da må vi lage et par varianter og justere underveis, sier Vikse.
Å lage små rundinger er nok det mest utfordrende
Hans Martin Vikse
Tester ut ideer med forskerne
Å lage deler selv sparer også UiB for kostnader. En rull med plast på 750 gram koster 3-400 kroner og varer til mange deler.
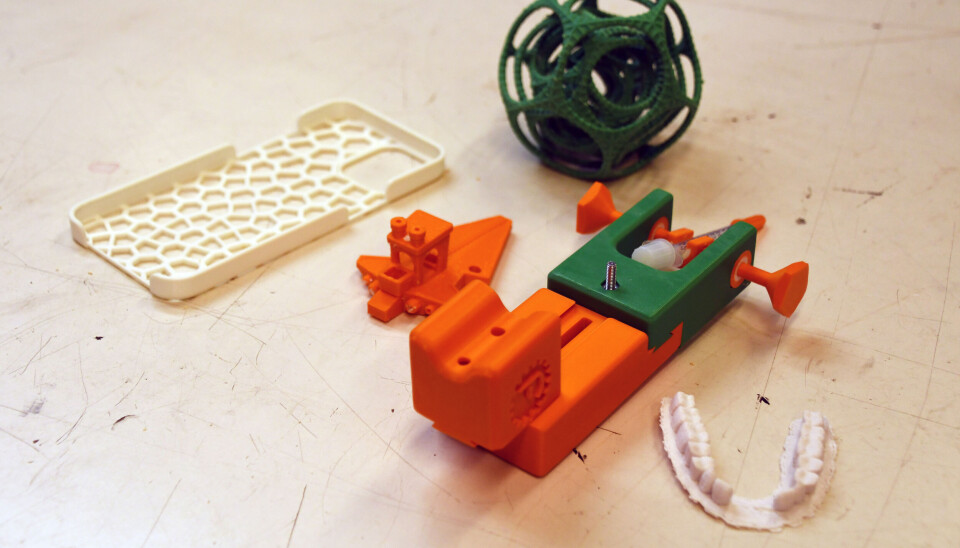
– Iblant kommer også forskerne til oss med en idé om noe som de ønsker at vi skal teste ut. Iblant fungerer det, og andre ganger ikke, det kommer an på presisjonsnivået. Eller så har de funnet deler på nettet som egentlig koster endel, og så kan vi heller lage det her, sier Vikse.
Det er veldig praktisk å ha en 3D-printer i nærheten når vi trenger en ny del med en gang
Forskningstekniker Stein Rune Lindhom
Et eksempel er en del til en maskin som skal holde fast i fortenner til forsøksmus. Den kostet egentlig 2500 å kjøpe ny, men kunne printes til under en krone.
– Det er også veldig praktisk å ha en 3D-printer i nærheten når vi trenger en ny del med en gang. Istedenfor å finne ut hvor du kan få tak i delene, gå gjennom hele bestillingsprosessen og vente ukevis på at den skal leveres, kan vi sette oss ned, tegne det ut og printe den på en dag. Det sparer mye ressurser, sier Lindhom.